The logistics sector is about to undergo a dramatic change. Warehouse operations are being rapidly transformed by automation and robotics, which offer increased productivity, precision, and efficiency. Although there is no denying the advantages of these developments, there are worries about how they may affect work for people. This blog article explores the growing usage of robotics in warehouses, the possible effects of automation on jobs in logistics, and the importance of workforce upskilling in order to survive in this changing environment.
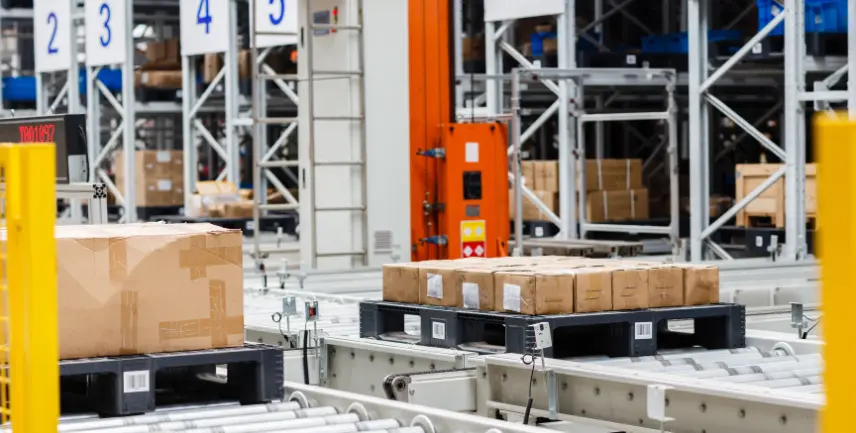
Logistics’ Automation Footprint
These days, warehouses are used by more than just humans. Repetitive operations like picking and packing, item sorting, and forklift operation are increasingly being performed by robots. Automated Guided Vehicles (AGVs) move cargo and optimize processes through self-navigating warehouses. Several reasons are responsible for these advancements:
- Enhanced Efficiency: Automation ensures faster and more reliable order fulfillment by removing human error and weariness.
- Lower Costs: Since robots can work around the clock, manpower and other operating costs can be significantly reduced.
- Increased Safety: Tasks that are dangerous or physically taxing can be automated to lower workplace injuries and provide a safer working environment for humans.
The Changing Nature of Jobs in Logistics
It is inevitable that some occupations will be lost to automation, despite the fact that automation has many benefits. An increasing number of repetitive jobs that have historically been completed by humans will be automated, which could result in job losses in some sectors of the logistics workforce.
But it’s crucial to approach this change from a neutral standpoint. The goal of automation is not to completely replace the workforce with humans. Rather, the goal is to develop a novel framework for human-robot cooperation.
Increasing Workforce Skill: The Secret to Adaptation
Logistics will be dominated by a workforce of the future, one that can operate harmoniously with robotic colleagues. Initiatives aimed at upskilling the workforce are essential to preparing it for these changing needs. This could appear like this:
- Technical Skills Training: To operate, maintain, and debug automated systems, personnel will need to be equipped with skills in robotics, automation technologies, and data analytics.
- Critical Thinking and Problem-Solving: Human workers will be required to perform more and more difficult problem-solving, critical thinking, and decision-making as automation takes care of mundane jobs.
- Collaboration and Communication: It will be crucial for people and robots to collaborate and communicate effectively. Employees will need to be skilled at deciphering system outputs and interacting with automated systems and coworkers in an efficient manner.
- Data Analysis and Interpretation: To optimize operations and spot chances for improvement, personnel with the ability to analyze and interpret the massive amounts of data generated by automated systems will be needed.
A Shared Responsibility
A multi-stakeholder strategy is responsible for upskilling the logistics workforce:
- Governments: Legislation can encourage cooperation between academic institutions and the logistics sector and provide incentives for training initiatives.
- Logistics Companies: Logistics companies can demonstrate their commitment to employee development and assure a staff that is ready for the future by investing in upskilling programs for their current workforce.
- Academic Institutions: To incorporate the skills necessary for the evolving logistics sector, academic institutions must modify their curricula.
- People: A mindset of perpetual learning and a proactive pursuit of opportunities for upskilling will be necessary for people to prosper in the automated logistics of the future.
A Future of Collaboration and Innovation
Automation presents a transformational opportunity rather than a threat to the logistics workforce. The logistics sector can take advantage of automation while maintaining a workforce that is knowledgeable and flexible by supporting upskilling programs and encouraging human-robot collaboration. In the future of logistics, people will not need to be replaced; rather, they will be given the tools they need to collaborate with robots more intelligently and productively. This cooperative strategy will open doors to a logistical environment that is more inventive, creative, and efficient.
Conclusion
Logistics will inevitably be impacted by automation. But the future of logistics might be bright if upskilling programs and human-robot collaboration are prioritized. The logistics sector can leverage the potential of automation to reach new heights of efficiency and creativity with a workforce that is knowledgeable and flexible.